Two color molds as two color molding products processing the most important molding equipment. Its quality is directly related to the quality of products. Moreover, because the mold in the two color molding processing enterprise production cost occupies a large proportion. Its service life directly affects the cost of two color molded products. Therefore, to improve the quality of two color molds, and maintenance of molds, to extend its life cycle, is the two color molding products processing enterprises to reduce costs and increase the benefits of important issues.
If the preservation of the mold is not enough attention, so that the mold in the preservation period of rust, surface finish degradation and other phenomena, resulting in product quality degradation, scrap rate is high, and some of the molds are even difficult to reuse, the need to re-invest a lot of money to procure a new mold, resulting in a great waste.
Data show that the use and maintenance in the mold service life factors affecting 15% to 20%. Two-color injection mold service life can generally reach 800,000 times, some well-maintained two-color molds can even be extended 2 to 3 times.
Therefore, the maintenance of two color injection molds is very important, as follows:
Daily maintenance in continuous production process
First level maintenance: clean and lubricate of mold parting surface and moving parts.(every 6-12 hours)
- Parting surface: Wipe the stains, dust, etc. on the mould outer surface and parting surface with a clean cotton cloth.
- Guiding system: Wipe the guide parts of the mold, such as guide pin, guide bush, with a clean cotton cloth, and apply lubricating oil to ensure smooth operation of the mold
- Ejection system: eject with normal stroke, and wipe clean, add oil on ejectors.
- Keep mold in dry to avoid rust: Timely dry the condensate generated in the process of mold production by using air gun.
Periodic maintenance in continuous production process
Second level maintenance: disassemble some parts for maintenance that will affect product quality, mold life and activities. (every 10k-20k shots or every week)
Third level maintenance: disassemble all the detachable parts for cleaning and maintenance, and replace the wear parts and aging parts. (every 200K shots or 6 months)
Prepare the maintenance tools in advance (such as hexagon wrench, lubricating oil, spare parts box, etc.)
Mould disassembling:
- Check each number of the plates before disassemble the mold, and re-confirm the number if there is any unclear, to ensure that you are able to assemble the mould again in right way after disassemble.
- Check the mold cooling channel with air gun, and dredge in time if insufficient flow or blockage is found
- Remove mold auxiliary mechanism (such as cylinder, hydraulic motor, mold foot, etc.) before disassemble the mould, and keep them properly.
- Disassemble the moving side fixing plate, ejector plate, bearing plate, cores and plates in turn. Before each step, you have to learn the internal structure, screw function, whether the parts have corresponding numbers, etc., to prevent the parts be damaged during disassemble.
Cleaning the mold parts and surface
- The rust and dirt on mold surface and plate can be removed by using whetstone with kerosene or diesel , and dried with cotton cloth to ensure the air venting effect of the mold surface;
- The waste oil and dirt on mold core sliders, guide pins, bearings, gears and other accessories can be removed by brush with mold detergent , reduce the interference of mold operation.
- Clean the dirt in the air venting groove and hole, if found some area be burned, it can be cleaned by using whetstone with kerosene or diesel, and increase the air venting groove properly;
Mold parts repair and replacement:
- Check springs, ejector pins etc. during mold disassembly and cleaning, if found any damage and wear, it should be replace in time.
- Check the wirings, repair or replace the damaged parts in time.
- Check the marks on mould, if any wear or miss, have to replace or repair.
Maintenance for short time shutdown (within 4 hours)
—without take off the mould from machine
- Turn off cooling water chiller
- Spray with some Oil-based release agent
- Ejectors backward to protect springs
Maintenance for weekend shutdown
—without take off the mould from machine
- Turn off the water valve, dry and clean the mould surface
- Spray with enough Oil-based release agent
- Ejectors backward to protect springs
Maintenance after a batch production
—Take off mould from machine and put mould to warehouse
- Take off water pipes, must dry the water inside the cooling channels by air blow enough time.
- Clean and dry the mould parting surface, spray with enough anti-rust agent.
- Clean and dry the mould out surface, spray with enough anti-rust oil, wrap with film to avoid rust.
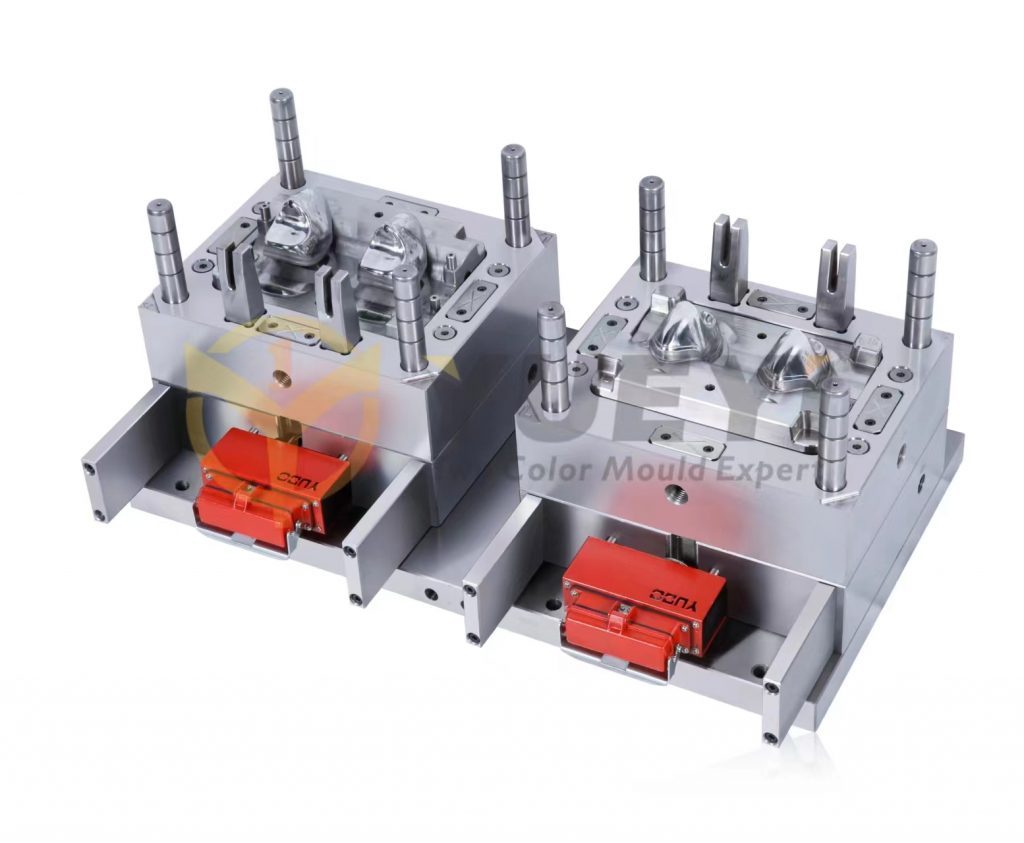
A pair of well-maintained molds can shorten the mold assembly, test run time, reduce production failures, make the production run smoothly, ensure product quality, reduce scrap loss, and reduce the operating costs and fixed asset investment, when the next production cycle begins, the enterprise can successfully produce products of qualified quality.
Leave A Comment