When it comes to injection molding, hot runner and cold runner gates have long been the subjects of heated debate among manufacturers. The choice between these two systems has traditionally revolved around factors like cycle times, material flow, and cost-effectiveness. In this article, we delve into the cost-effectiveness of hot runner and cold runner gates from a fresh and unconventional perspective, shedding light on how these decisions can make or break your bottom line.
Hot Runners: The Precision Performance
Hot runner systems are celebrated for their precision and efficiency in molding high-quality products. They offer the advantage of eliminating the need for runners, reducing material waste, and ensuring the production of consistent, top-tier parts. This reliability has a profound impact on the cost-effectiveness of the overall production process.
One aspect of cost-effectiveness often overlooked in the hot runner vs. cold runner debate is the long-term return on investment (ROI). While hot runner systems may involve a higher initial investment, they can pay off handsomely in the long run. Reduced material waste, minimal rework, and shorter cycle times translate to increased output and decreased production costs per unit.
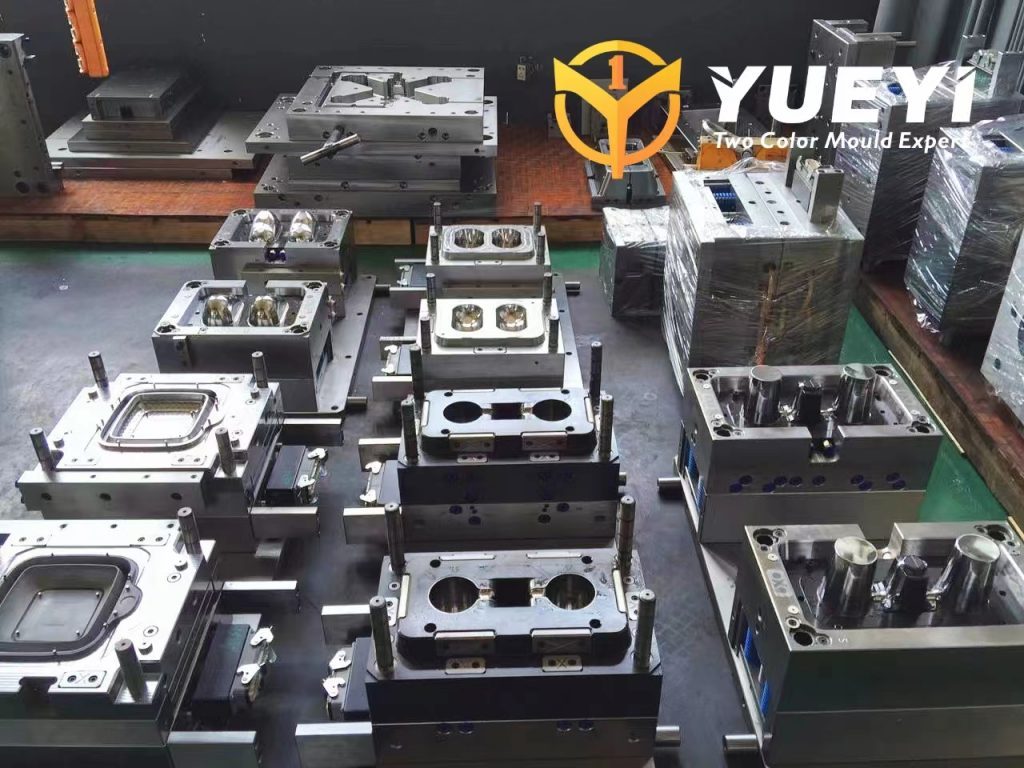
Cold Runners: The Pragmatic Alternative
Cold runner systems offer a pragmatic approach to injection molding, especially for applications where material versatility is a key consideration. The versatility of cold runners, which can accommodate various plastics, can significantly reduce the need for specialized molds and materials. This can lead to cost savings, particularly when dealing with a diverse product line.
Moreover, cold runners often require less maintenance and are quicker to set up, resulting in lower labor costs and reduced downtime. These operational advantages contribute to the overall cost-effectiveness of cold runner systems.
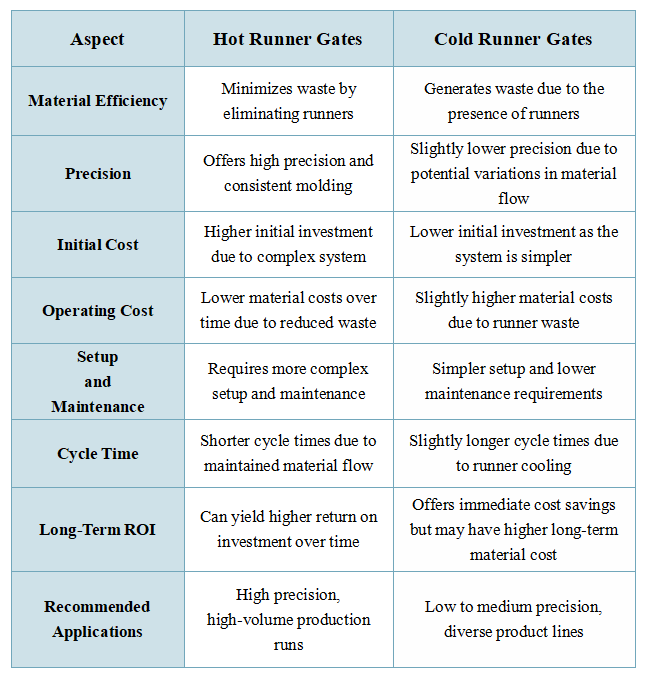
The debate between hot runner and cold runner gates is far from one-dimensional. While hot runners offer precision and long-term cost-effectiveness, cold runners provide flexibility and efficiency.
Ultimately, the decision between hot and cold runner systems should be made with a comprehensive understanding of the specific needs of the project at hand. By focusing on cost-effectiveness from this unique perspective, manufacturers can optimize their production processes and drive profitability while delivering high-quality products to the market.
Leave A Comment